Setting Up Your Lab
How to plan space for your digital lab.
Space is the primary consideration in setting up any lab. For those creating a lab from scratch, this will be easier. For those with an existing lab, it will be more difficult because many owners will find it hard to eliminate analog components that really serve no useful purpose, but “have value” or “might be used” someday.
Walk through your workflow.
An easy way to consider the space requirements is to mentally walk through the workflow in your mind, understanding that there are usually multiple different workflows that will occur. Then create a map of the lab and plot out the physical dimensions of the equipment space, workspace, storage space, and movement space. Three common workflows to consider are in-house aligner fabrication, digital indirect bonding, and soldered/welded appliance fabrication. The information below will use the in-house retainer/aligner fabrication, 3D printing brackets and DIB trays as an example.
Four types of spaces need to be considered:
Counter Space for Equipment | Counter Space for Work | Storage Space | Movement Space
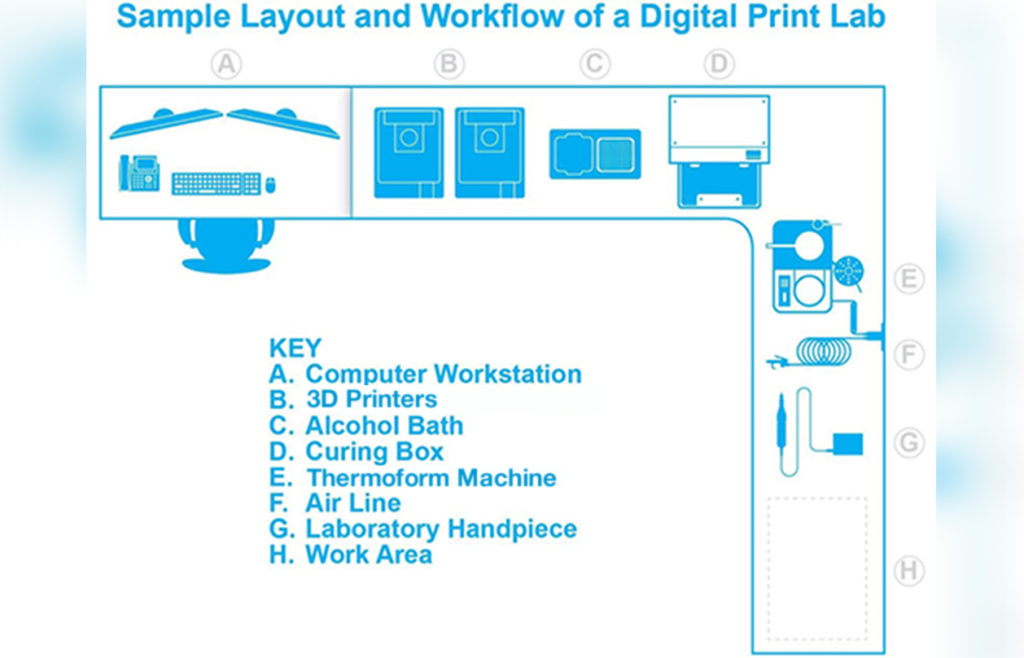
Counter Space for Equipment
For physical equipment, most manufacturers have footprint and height dimensions available. Equally important is the dimension of the equipment while in use. For example, 3D printers are static while printing, but the printer must be opened to add liquid resin or to remove the printed model. Some printers open vertically others open horizontally; so overhead space or lateral space may need to be considered depending on the printer.
The most common pieces of physical equipment used in a digital lab that occupy counter space include:
Counter Space for Work
The most common work areas include:
Storage Space
Another space consideration is that of storage. Some items will be used frequently and are stored in drawers for easy access, while others that are used less frequently can be stored in cabinets or closets.
Movement Space
The amount of space required will depend on how many lab technicians may need to be in the space at any given time. It is important to plan for the future, and consider if multiple people will need to pass by each other in the lab.